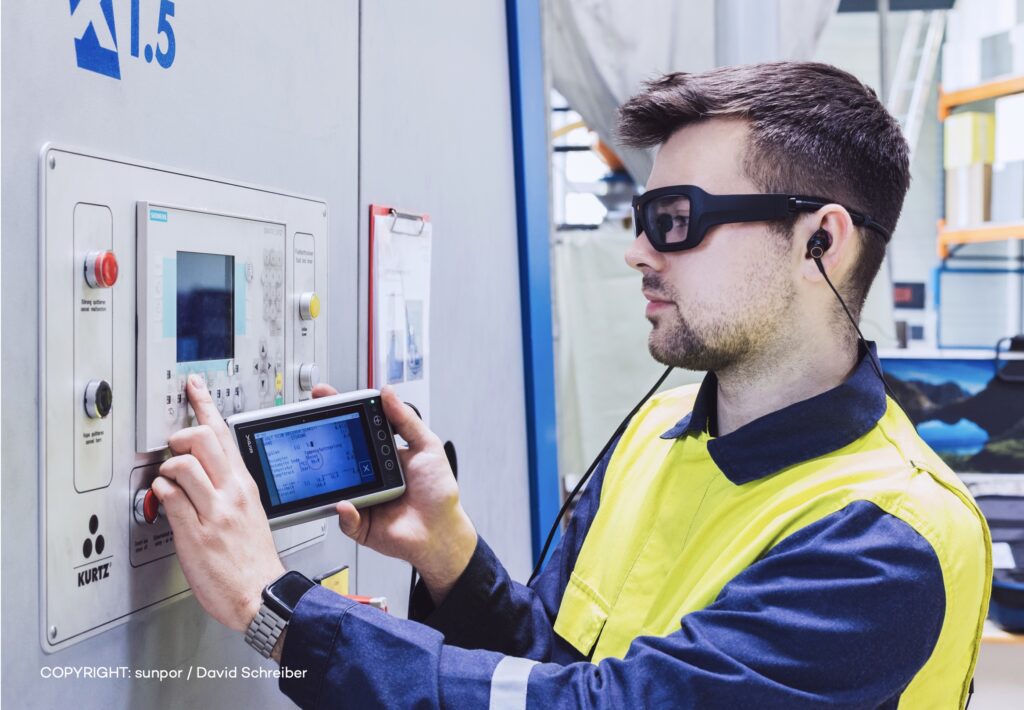
By Viewpointsystem Editorial Team
Despite a slight slowdown in inflation, the manufacturing industry will face significant challenges in 2024. Products, raw materials and services have become more expensive at all levels of the supply chain. At the same time, these challenges offer opportunities to become more resilient in the marketplace and to leverage the potential of digital tools and technologies. High energy prices and rising labor costs are not only a burden, but also an opportunity for change.
Experts predict pressure on the industry in three other areas:
Workforce: Demographic challenges are expected to intensify in 2024. The ongoing wave of retirements is creating acute shortages in key roles, from engineering to production.
Sustainability: In the coming years, the pressure on companies to take action on climate change and improve the overall sustainability of their operations will continue to increase.
Pace of innovation: In many industries, companies are facing faster development cycles and constant pressure to innovate to stay ahead of the competition.
Faced with these challenges, industrial companies are forced to improve efficiency, reduce costs, and, at the same time, increase innovation and competitiveness.
Remote service solutions, such as remote support and remote maintenance, are emerging as allies in achieving these ambitious goals. Technical services are provided remotely without the need for a service technician to visit the site in person. In more complex scenarios, remote support helps troubleshoot problems. Equipping field workers with smart glasses allows them to keep their hands free and focus on the task at hand.
Eight reasons to invest in remote service solutions:
#1: Increased efficiency
Remote support enables rapid diagnosis and resolution of issues without the need for a physical on-site presence. Using the camera of the employee’s smart glasses on-site, the remote expert can see exactly what the employee is seeing and guide them through the problem resolution process. The result is reduced downtime and increased overall efficiency. Manufacturers and service providers can pool staff, expertise and infrastructure, paving the way for efficient service delivery.
#2: Cost savings
Eliminating the need for technicians and experts to travel leads to significant cost savings. This includes not only travel and labor costs, but also reduced machine or plant downtime.
#3: Leverage global expertise
Remote support allows companies to access expertise from all over the world to solve problems even in remote locations. Virtual support ranges from initial diagnosis to help with complex problems from centrally located service technicians or other experts. This allows industrial companies to better distribute their expertise and provide support where specialists are not available.
#4: Improved customer loyalty
Quick responses to customer inquiries and avoidance of extended downtimes strengthen customer loyalty and satisfaction. Manufacturers can expand their business models with product-related remote service offerings.
#5: Proactive maintenance
Continuous monitoring helps identify and resolve potential problems early, preventing serious failures.
#6: Promote sustainability
By reducing travel, companies can improve their environmental impact and promote more sustainable business practices.
#7: Scalability and flexibility
Remote services scale easily to accommodate different business sizes and environments. They provide the flexibility to adapt to evolving business needs.
#8: Competitive advantage through digitalization
Remote services are a critical aspect of the digital transformation of industrial companies, strengthening their competitiveness. The integration of additional technologies, such as connected machines, AI and machine learning, enables advanced monitoring and diagnostic solutions that increase the efficiency of remote services.
Conclusion
Investing in remote services is more than just a technological adaptation; it is a strategic move to meet today’s challenges. By embracing these innovative services, industrial companies can not only increase efficiency and optimize costs, but also strengthen their resilience to future challenges.
Find more information on remote support and remote maintenance using smart glasses here.
REFERENCES
AutomationNEXT, “Ausblick 2024: Wie sich der Druck für die Industrie verändert”, 14.12.2023.