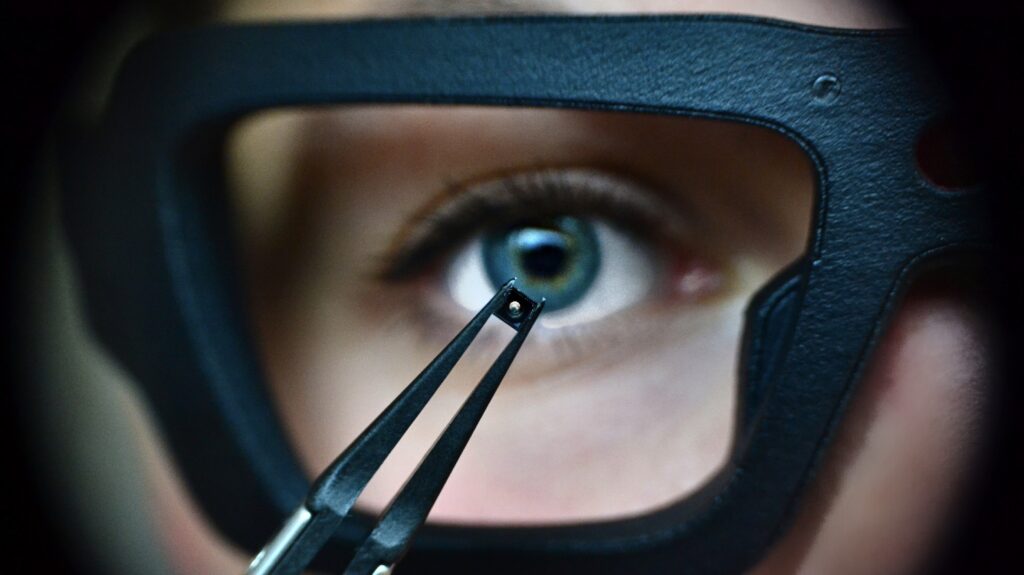
By Jana Riethausen, Viewpointsystem Editorial Team
Micro-optics are fundamental components in camera systems for smart devices, mobility applications, or medical products. These tiny lens systems, ranging from just a few micrometers to millimeters in size, also play a crucial role in areas such as endoscopy, 3D sensors, and biometric identification systems. They are seen as the key to further product innovations.
Innovative micro-optics of outstanding quality at competitive prices – the joint project “3DPrintoptixMarket” of Viewpointsystem and the Stuttgart-based company Printoptix addresses exactly this market need. Using a novel 3D printing process, high-end micro-optics are manufactured in a single step. These optics will be used in Viewpointsystem’s smart glasses to enable individual product customization and further enhance the user experience. The goal is to increase production speed and make the optics suitable for industrial mass production.
Our interview with Nils Fahrbach, CEO of Printoptix, and Frank Linsenmaier, CTO of Viewpointsystem, provides insight into this ambitious, EU-funded project.
EDITORIAL TEAM: THE MANUFACTURING PROCESS OF MICRO-OPTICS IS CONSIDERED TO BE EXTREMELY CHALLENGING. CONVENTIONAL MANUFACTURING TECHNOLOGIES OFTEN REACH THEIR LIMITS, WITH A REJECT RATE OF UP TO 40% IN THE PRODUCTION OF SUCH SYSTEMS, GIVEN THE HIGH PRECISION REQUIRED. HOW DO YOU ACHIEVE RELIABLE PRODUCTION AND AVOID DEFECTIVE PRODUCTS?
Nils Fahrbach: The 3D printing process we use produces complete, often multi-lens optics in a single step. This reduces the risk of errors significantly since there is only this one step. If, for some reason, this single process were to fail, which can naturally happen in any production due to external factors, we are not dependent on suppliers or upstream processes to manufacture individual components.
Instead, we can simply restart 3D printing on the spot, possibly with adjusted parameters. In the event of a failure, we can respond very quickly to ensure reliable production and delivery.
DOESN’T THE USE OF POLYMER LENSES RESULT IN A LOSS OF QUALITY? CAN PLASTIC MATERIALS COMPETE WITH GLASS?
Nils Fahrbach: Absolutely, the use of polymer lenses does not lead to any disadvantages in optical quality for the applications we are targeting. It’s worth noting that even high-quality cameras in smartphones mostly use lenses made of plastic materials.
Polymer lenses have different optical and mechanical properties than glass lenses and are not suitable for use in high-power lasers, for example. However, this is irrelevant to the applications we are targeting in this project.
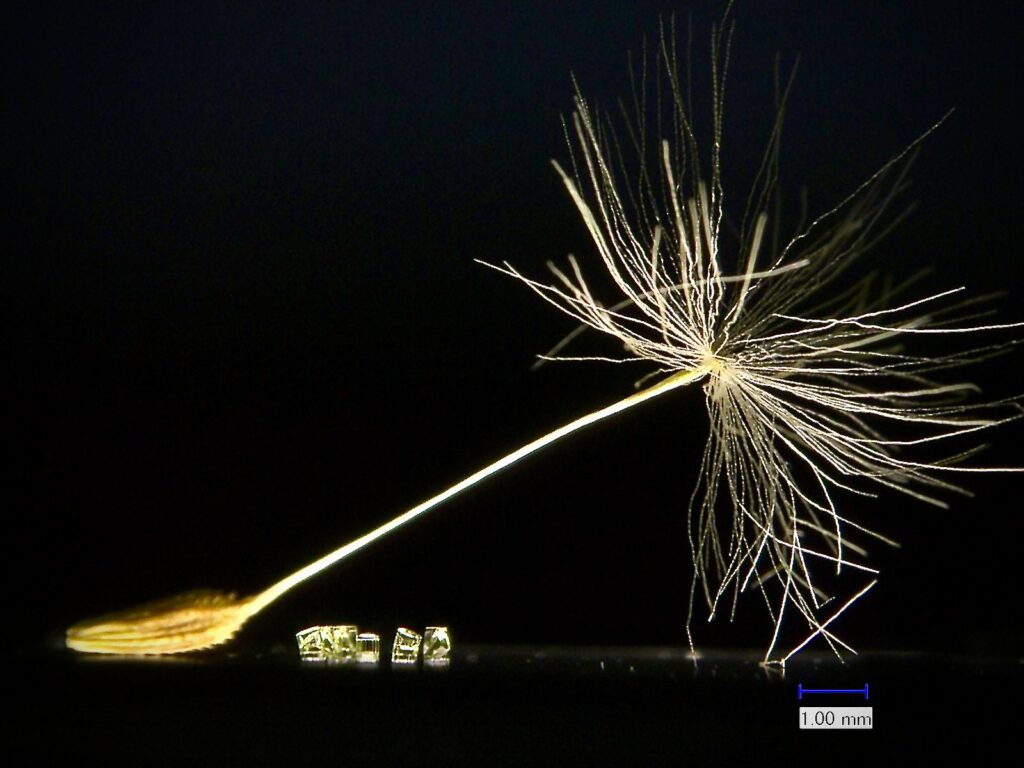
HOW SUITABLE IS YOUR 3D PRINTING PROCESS FOR INDUSTRIAL MASS PRODUCTION?
Nils Fahrbach: 3D printing is a young production method with enormous potential for efficiency improvements. It is a serial process, meaning we produce one part at a time, rather than manufacturing many parts simultaneously, as some other methods do.
To offer competitive mass production, the 3D printing process must be very fast for each individual part. We have been successfully working on this for years. With the process time we have already achieved, we can currently produce smaller series of up to several thousand units at competitive prices. With the EU funding in this project, we now have the resources to reduce the printing time to a fraction of the current time within the next three years, enabling the production of complete optical systems in just a few minutes.
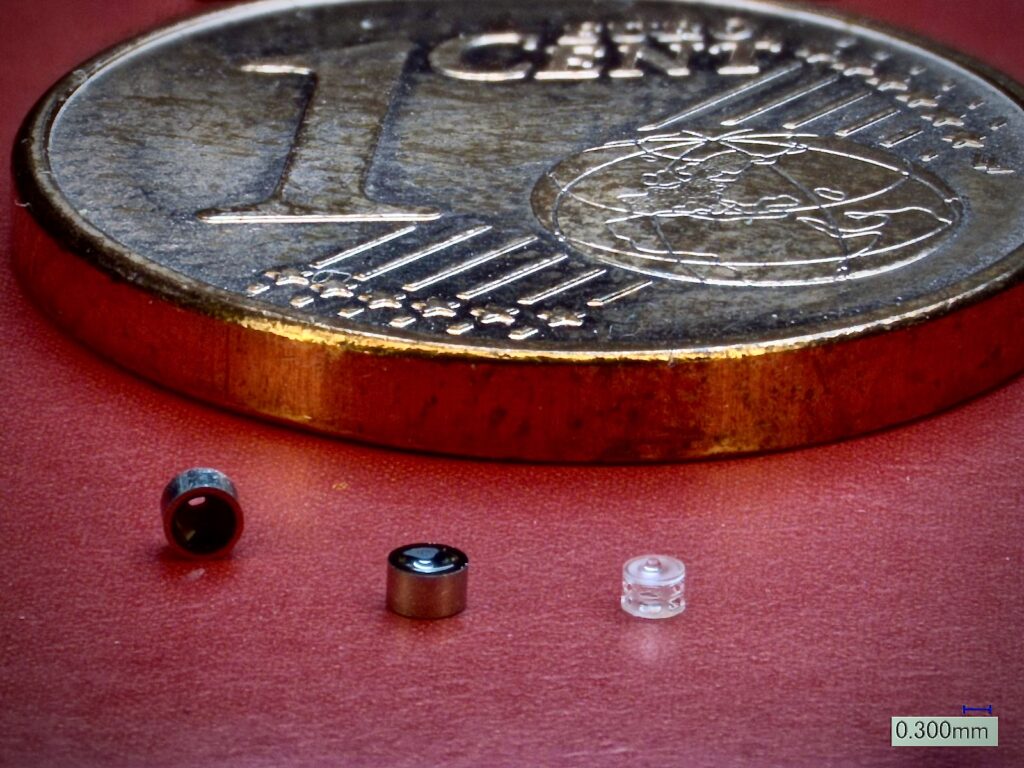
IN WHAT WAYS DO VIEWPOINTSYSTEM’S CUSTOMERS BENEFIT FROM THE 3D-PRINTED MICRO-OPTICS?
Frank Linsenmaier: In the long run, we aim to reduce our product costs. With 3D printing, it’s possible to produce on-demand, eliminating the need for minimum order quantities, large inventories, and ensuring short lead times for product modifications. This provides a cost-effective solution for our customers.
3D printing also offers remarkable flexibility in terms of applications and product design. The compact design gives our customers the ability to seamlessly integrate the technology into their own systems. Our long-term goal is to integrate sensors into customer systems, making them nearly invisible and cost-effective.
MASS CUSTOMIZATION AND INDIVIDUAL PRODUCT ADAPTATIONS ARE GOALS OF INDUSTRY 4.0. DOES THIS ALSO APPLY TO SMART GLASSES? DO YOU HAVE ANY APPROACHES OR SPECIFIC PROJECTS RELATED TO OPTICALLY CUSTOMIZED EYEWEAR?
Frank Linsenmaier: Yes, absolutely. The development of smart glasses is progressing rapidly. Industrial smart glasses have completely different requirements than consumer applications, and research environments require different data than military applications.
This diversity of customer requirements leads to many product customizations and variations. With custom designs, we can meet these needs more easily and quickly than other OEMs.
WHEN WILL THE FIRST 3D PRINTED OPTICS BE USED IN VIEWPOINTSYSTEM’S SMART GLASSES?
Frank Linsenmaier: As soon as possible. The first tests are already very promising! Of course, further tests are needed to confirm the technology’s robustness, and the optics will need to be integrated into our overall product architecture.
TWO ISSUES THAT ARE ON THE MINDS OF MANY COMPANIES ARE SUSTAINABILITY AND THE EU SUPPLY CHAIN ACT, WHICH HAS ALREADY COME INTO EFFECT IN GERMANY. CAN PRINTOPTIX’ PRODUCTION TECHNOLOGY SUPPORT EFFORTS IN THIS AREA?
Nils Fahrbach: Absolutely. We offer complete development and production under one roof in our Stuttgart production facility, without being dependent on suppliers or service providers from third countries. The only things we purchase externally are the 3D printers themselves and the raw materials, both from Nanoscribe in Karlsruhe.
3DPrintoptixMarket is funded over a three-year period by the European Innovation Council, Europe’s flagship innovation program to identify, develop and scale up breakthrough technologies and game-changing innovations.
For more information: www.3Dpom.eu
