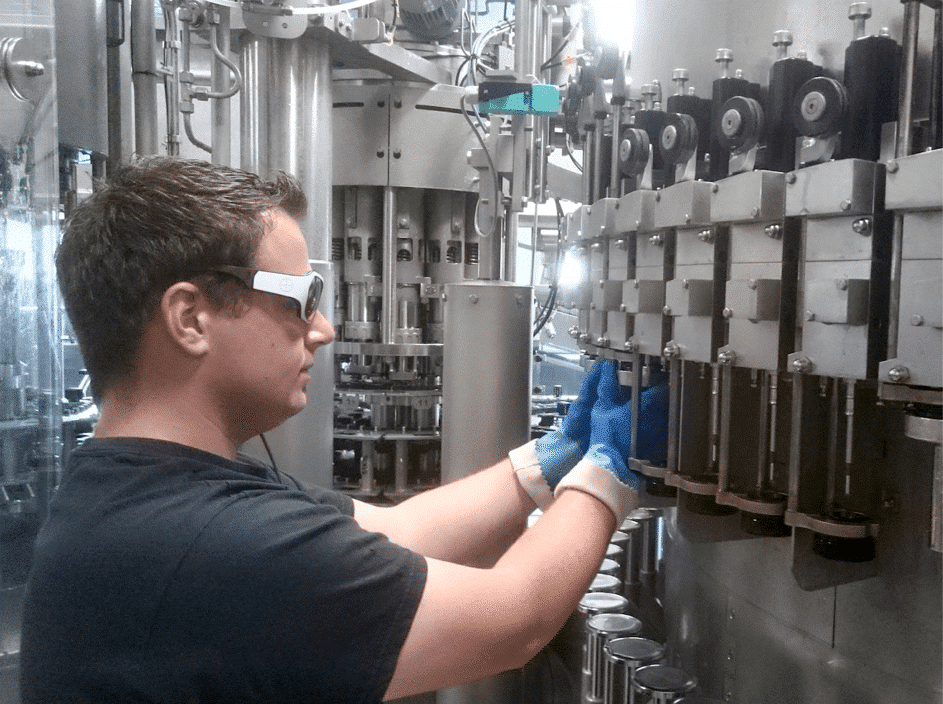
By Sven Hugo Joosten
Let’s start with a practical sample calculation: The machinery at a large bottling plant in the drinks industry has ground to a halt. For every hour of downtime more than 23,000 bottles will not be filled, equating to lost turnover of approx. 33,000 euros. The workers on site cannot rectify the fault and a specialist from the parent plant will have to be brought in. Including the time required for travel and preparations, it will usually be 12 hours before the specialist is on site and can rectify the fault – leading to a total loss of turnover of 400,000 euros.
Hardly surprising therefore that downtimes and production stoppages are an absolute horror scenario for managers, and it’s probably no different at your company either. Given the increasingly lean and centralised structures in industry today, the expert you need is often far away when swift action is required. Providing complex fault diagnoses and instructions is almost impossible over the telephone.
However, if your technician has immediate access to expert assistance your company can save a fortune. This is made possible by the immediate four-eyes principle with Remote Support. If for example, the bottling line has come to a standstill, the data glasses worn by the technician live stream images of the malfunction to the specialist at a remote location who can then make a rapid diagnosis. The integrated eye-tracking offered by our VPS 16 enables malfunctions to be identified and corrected smoothly and swiftly: By tracking the on-site technician’s eye movements, the glasses allow the in-house expert (or technical supplier’s customer support) to see on his screen exactly where the technician is looking and then to give precise instructions. Instead of long and complicated descriptions like “the fifth cable from left at the back” eye tracking means it takes just one look to know which cable or machine part is meant. This saves both time and nerves, especially where complex processes are involved. Slip-ups that cause further damage are avoided.
But notwithstanding the fascination of what the technology has to offer: You must make sure that the glasses you use are functional, robust and also comfortable to wear for hours at a time. Many smart glasses deliver reliable results in the development lab – but just not in industrial environments where they run up against changing light conditions, temperature fluctuations, dust and dirt. Packed full of technology they are so heavy that wearers can find it impossible to work for lengthy periods of time with the necessary concentration. Often, they even cause pressure sores on the nose after just a short period. You should therefore consider very carefully which technical features really make sense for your company while guaranteeing the full functionality of the glasses.
And finally, to go back to our sample calculation: Reducing downtime from 12 hours to just one hour, a realistic figure in our experience, equates to cost savings of 367,000 euros. And: Travel expenses and downtime costs for hastily dispatched experts are not even incurred in the first place.
This video explains how Remote Support from Viewpointsystem works:
Author:
Sven Hugo Joosten has been fascinated by new technologies since he was a little boy but first began his career in sales and marketing in the clothing and entertainment electronics sectors. In 2017 he joined Viewpointsystem as Head of Sales. After work Sven enjoys going to the theatre, the fitness studio or riding his trekking bike. At weekends, he likes to relax by going hiking in the mountains.