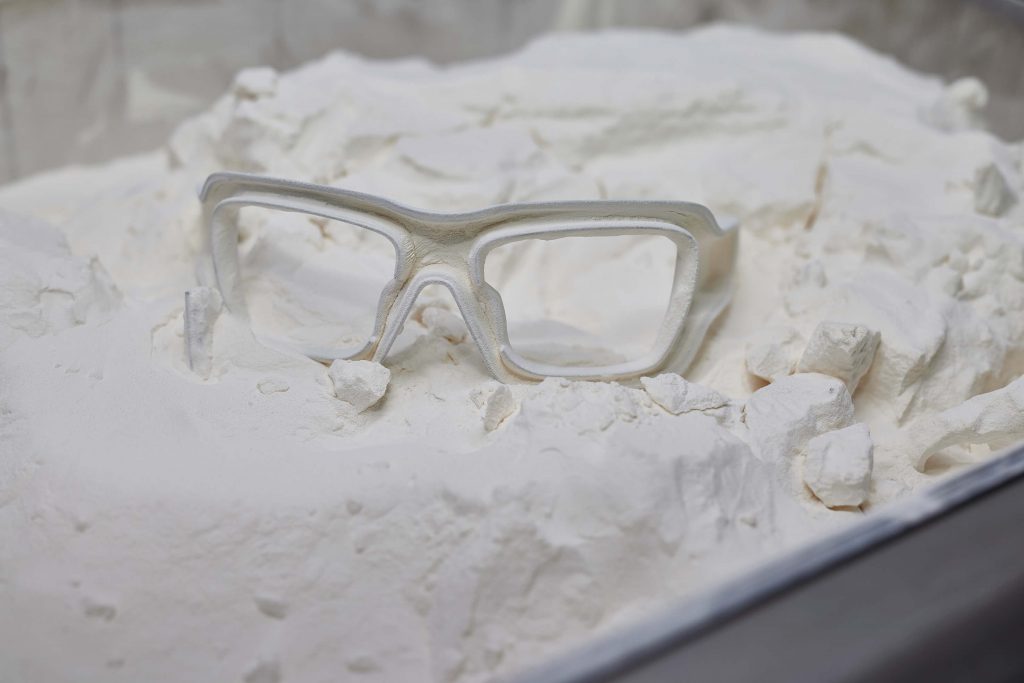
An insight into our production
By Lukas Porak, Head of Production
It wasn’t long ago that 3D printing was used primarily for the inexpensive production of prototypes. In the meantime, the technology has matured and, thanks to enormous qualitative improvements, has arrived in industrial series production. In our production facility just outside Vienna, we have set up a production line in cooperation with our partners HP and d4pro. This makes us one of the first companies in Austria to leave the path of classic injection molding production and break new ground.
A total of 12 components of our smart glasses are produced additively, from the carrier frame to the front cover, the nose pads and internal technical parts. After just a few hours, we can take the components out of the powder bed of the printer’s build unit for further processing. Within just 24 hours, we can make adjustments to the frame and optimize the design. In traditional production, such changes often take several months. This is because the necessary molds and tools first have to be produced and the next production cycle has to be awaited.
Additive manufacturing thus significantly shortens our innovation cycles. For us as a young company in a dynamic technology environment, this means a major competitive advantage. We can make bold changes and try things out of the box, even with the risk of failing. Because with additive manufacturing, we can produce on demand and in smaller batches, at comparatively manageable costs. We have our own factory in-house, so to speak. This means we don’t have to buy in large quantities in advance and can save on storage capacity, which is as sustainable as it is economically sensible.
Another major advantage is that we can extrapolate directly from the prototype to the series product. We know exactly how it will look and behave in the end, whereas with conventional production processes there are usually certain deviations between the prototype and the finished series product.
Now let’s take a closer look at the actual production process. This is how the additive manufacturing of our smart glasses works:
The industrial 3D printer prints ultra-thin layers of plastic powder layer by layer. Each layer is about as thin as a human hair. These many layers create smart glasses frames with very high density and low porosity. They are therefore very stable and ideally suited for use in practical working environments such as in manufacturing. Printing is done with two different liquids, the so-called “Agents”: The Detailing Agent provides the edges and the optimal surface. The Fusing Agent fuses the powder layers by means of heat. More than 30 million fine drops are printed into the powder bed per second.
After the printing process, which takes between eight and twelve hours, the build unit with the blanks in the powder bed is pushed into the connected processing unit for cooling. The cooling process takes between five and 25 hours. After this, the excess powder is extracted. It can be used for a new printing process. Only 20 percent new powder has to be added.
After cooling and cleaning, the smart glasses blank is blasted with tiny glass beads in a blasting cabin (“glass bead blasting”). This removes any residual powder and densifies the surface. The subsequent impregnation process colors the blank and densifies and refines its surfaces with polymer bead blasting. All materials used are certified biocompatible and thus neutral to the skin.
At the assembling station, the smart glasses carrier is assembled with the prepared electronics. Our self-developed high-performance electronics with camera technology and sensors are inserted into the carrier of the smart glasses. Finally, the carrier frame and the eyeglass cover are joined by means of a high-strength snap-on connection. The latter is the result of continuous optimization of our smart glasses geometries, which would not have been possible using conventional manufacturing processes.
After assembling, the VPS 19 smart glasses are ready for delivery to the customer. Additive manufacturing even gives us the opportunity to respond individually to customer wishes, for example if certain shapes are desired or even colors in the customer’s CI.