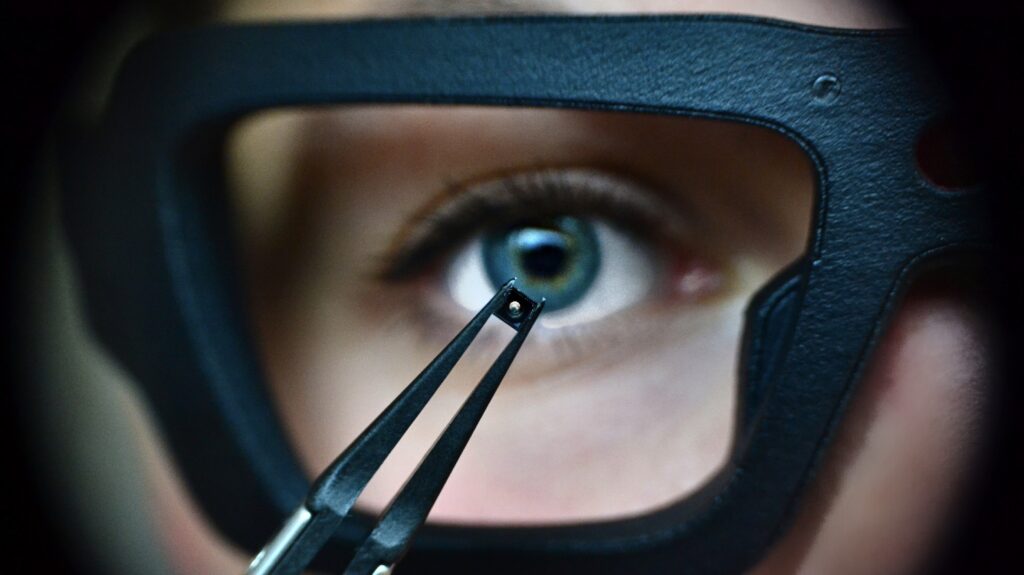
Tiny high-end optics, customizable and suitable for series production: Printoptix from Stuttgart and Viewpointsystem from Vienna aim to bring complex micro-optics to market. They focus on outstanding quality at competitive prices using a novel 3D printing process. Their ambitious cooperation project “3DPrintoptixMarket” is supported by the European Innovation Council (EIC) with a grant of 2.5 million euros. The micro-optics are intended for use in smart wearables, medical devices, and industrial applications.
Stuttgart/Vienna, August 24, 2023 –The unique 3D printing process by Printoptix aims at enabling the cost-effective and high-quality production of so-called “impossible parts” in the field of micro-optics. Tiny multi-component lens systems, including apertures and other elements, which would require numerous production steps and manufacturing machines using conventional methods, are manufactured in a single piece, using a single printing step with this method. This eliminates many intricate manufacturing stages, significantly simplifying and accelerating the production process.
“Our technology opens up entirely new design possibilities and free forms that would simply be unattainable using conventional manufacturing techniques,” says Nils Fahrbach, CEO of Printoptix. “This paves the way for technological innovations in areas such as medical endoscopy or augmented reality. Furthermore, the manufacturing process becomes more robust as the assembly and mechanical alignment of optical components are no longer necessary.”
Practical use in smart glasses
With Viewpointsystem as a project partner, the 3D-printed micro-optics are now being prepared for the market. The optics will be used in the smart glasses of the Viennese deep tech company and will be tested in practice by a number of industrial customers to allow for practical improvements. In addition, the possibilities for scaling and individualizing the production of micro-optics are being optimized.
“With smart glasses, it is important to be able to adapt the micro-optics to different face shapes and individual eye characteristics,” explains Frank Linsenmaier, CTO of Viewpointsystem. “The flexibility and personalization capabilities of the 3D printing process allow us to further improve our functionality and user experience at a manageable cost.”
The goal of the cooperation project is to reduce the micro-optics size by a further 50 percent while maintaining consistent optical quality. This will enable the components to be used in the smallest optical modules for augmented reality glasses. Furthermore, the printing time is expected to be reduced by more than 70 percent to less than ten minutes.
Fast product innovation without long supply chains
The flexibility and speed in production make 3D-printed micro-optics an attractive solution for companies and research institutions with smaller quantities as well as for major market players. It gives industrial companies the ability to add custom optical components quickly, easily, and affordably to their products.
“Products that typically require complex processes and often involve various suppliers from overseas will soon be available from us as a one-stop solution, right at your doorstep,” concludes Nils Fahrbach of Printoptix. “We are proud to contribute to the establishment of expertise and production structures in the field of micro-optics in Europe with this project.”
Printing micro-optics in one piece and in a single step
Optical components are subject to particularly high-quality demands. Drawbacks of 3D printing have included disruptions in volume and on the surfaces of printed objects, such as layer formation or roughness. The 3D printers used in the 3DPrintoptixMarket project, developed by Nanoscribe, now employ an innovative technique called grayscale lithography, which avoids the typical step effects of 3D printing while significantly enhancing printing speed.
With the 3D printing process perfected by Printoptix, it is possible on this basis to print entire optically smooth lens systems monolithically in one piece without the need for subsequent assembly with corresponding defects.
“While modern smartphone camera lenses, for instance, consist of up to seven individual lenses and also combine many extra parts such as apertures and retaining structures, the 3D printers we use produce a single transparent polymer piece. Through a patented process, it is equipped with apertures and a black protective casing in a single, straightforward step,” explains Dr.-Ing. Simon Thiele, CTO of Printoptix.
3DPrintoptixMarket is funded over a three-year period by the European Innovation Council, Europe’s flagship innovation program to identify, develop and scale up breakthrough technologies and game-changing innovations.
For more information: www.3Dpom.eu

Press release to download as pdf file.