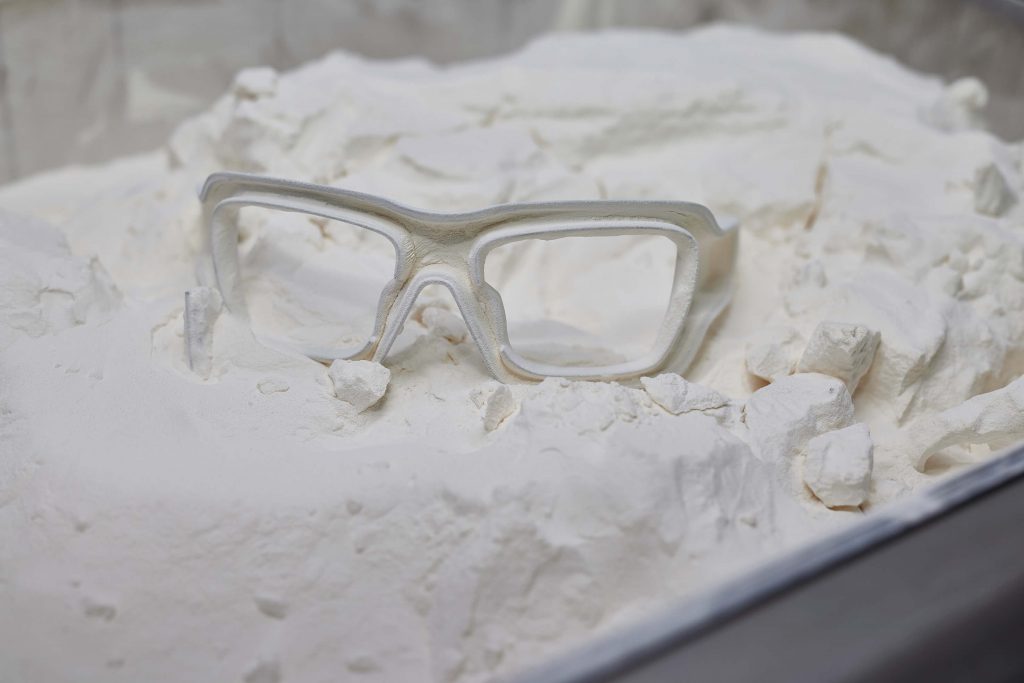
Ein Einblick in unsere Produktion
Von Viewpointsystem Redaktionsteam
Es ist noch nicht lange her, da wurde 3D-Druck vor allem zur günstigen Herstellung von Prototypen eingesetzt. Mittlerweile ist die Technologie erwachsen geworden und dank enormer qualitativer Verbesserungen in der industriellen Serienproduktion angekommen. Auch wir setzen auf die additive Fertigung: In unserer Produktion vor den Toren Wiens haben wir in Kooperation mit unseren Partnern HP und d4pro eine Fertigungsstraße eingerichtet. Damit sind wir eines der ersten Unternehmen in Österreich, das von der klassischen Spritzguss-Produktion absieht und neue Wege geht.
Insgesamt zwölf Komponenten unserer Smart Glasses werden additiv hergestellt, vom Trägerrahmen („Carrier“) über die Front („Stylecover“) bis hin zu den Nosepads und inneren technischen Teilen. Bereits nach wenigen Stunden können wir die Teile aus dem Pulverbett der Build-Unit des Druckers holen und weiterbearbeiten. Innerhalb von 24 Stunden können wir Anpassungen an den Brillenrahmen vornehmen und die Konstruktion optimieren. Bei der klassischen Produktion dauern solche Änderungen oft mehrere Monate, da zunächst die erforderlichen Gussformen und Werkzeuge hergestellt werden und der nächste Produktionszyklus abgewartet werden muss.
Die additive Fertigung verkürzt unsere Innovationszyklen somit erheblich, was für uns als junges Unternehmen in einem dynamischen Technologieumfeld einen großen Wettbewerbsvorteil bedeutet. Wir können mutig Veränderungen vornehmen und Dinge außer der Reihe ausprobieren, auch mit dem Risiko, damit zu scheitern. Denn im Gegensatz zum Spritzgussverfahren können wir bedarfsgerecht und in kleineren Serien produzieren, zu vergleichsweise überschaubaren Kosten. Wir haben sozusagen unsere eigene Fabrik im Haus. So müssen wir nicht auf Vorrat in großen Stückzahlen einkaufen und können Lagerkapazitäten einsparen – das ist so nachhaltig wie ökonomisch sinnvoll.
Ein weiterer riesiger Vorteil: Wir können vom Prototyp direkt auf das Serienprodukt schließen. Wir wissen genau, wie es final aussieht und sich verhält, während bei klassischen Produktionsverfahren in der Regel gewisse Abweichungen zwischen Prototyp und fertigem Serienprodukt liegen.
So funktioniert die additive Fertigung unserer Smart Glasses:
Von außen ist es nur zu erahnen: Der industrielle 3D-Drucker bedruckt Schicht für Schicht hauchdünne Kunststoff-Pulverschichten. Jede Schicht ist in etwa so dick wie ein menschliches Haar. Durch diese vielen ultradünnen Schichten entstehen Brillenrahmen mit sehr hoher Dichte und geringer Porosität. Sie sind also sehr stabil und bestens geeignet für den Einsatz in praktischen Arbeitsumfeldern – z.B. in der Produktion. Gedruckt wird mit zwei verschiedenen Flüssigkeiten – Agents genannt: Der Detailing Agent sorgt für die Kanten und die optimale Oberfläche. Der Fusing Agent ermöglicht das Verschmelzen der verschiedenen Pulverschichten mittels Hitze. Pro Sekunde werden über 30 Millionen feinste Tropfen ins Pulverbett gedruckt.
Nach dem Druckvorgang, der zwischen acht und zwölf Stunden dauert, wird die Build Unit mit den Brillen-Rohlingen im Pulverbett zum Abkühlen in die angeschlossene Processing Unit geschoben. Zwischen fünf und 25 Stunden dauert der Abkühlvorgang. Danach wird das überschüssige Pulver abgesaugt. Es kann für einen neuen Druckvorgang verwendet werden. Lediglich 20 Prozent neues Pulver müssen hinzugegeben werden.
Nach dem Abkühlen und Reinigen wird der Brillenrohling in einer Strahlkabine mit winzigen Glasperlen abgestrahlt („glass bead blasting“). So wird anhaftendes Restpulver entfernt und die Oberfläche verdichtet. Das anschließende Imprägnier-Verfahren färbt den Rohling und verdichtet und veredelt seine Oberflächen mit Polymer-Perlstrahlen. Alle verwendeten Materialien sind zertifiziert biokompatibel und damit nachweislich neutral zur Haut.
Zuletzt erfolgt das Zusammenfügen des Brillen-Carriers mit der vorbereiteten Elektronik an der Assembling-Station. Unsere selbst entwickelte Hochleistungselektronik mit Kameratechnik und Sensorik wird in den Carrier der Smart Glasses eingesetzt. Zuletzt werden Trägerrahmen und Brillen-Cover mittels einer hochfesten Schnappverbindung gefügt – ein Resultat stetiger Optimierung unserer Brillen-Geometrien, welche mit klassischen Fertigungsverfahren nicht darstellbar wäre.
Fertig! Nach dem Assembling sind die VPS 19 Smart Glasses fertig zur Auslieferung an die Kunden. Die additive Fertigung gibt uns sogar die Möglichkeit, individuell auf Kundenwünsche zu reagieren, beispielsweise wenn bestimmte Formen oder auch Farben in der Kunden-CI gewünscht sind.